How Digital Twins Benefit Industrial Manufacturing: Cost Reduction, Predictive Maintenance & More
In an era where efficiency, speed, and adaptability define success, digital twin technology is revolutionizing how factories operate. More than just a buzzword, digital twins are becoming a crucial component in the future of smart manufacturing — helping companies optimize operations, reduce costs, and make better decisions.
3/27/20252 min lesen
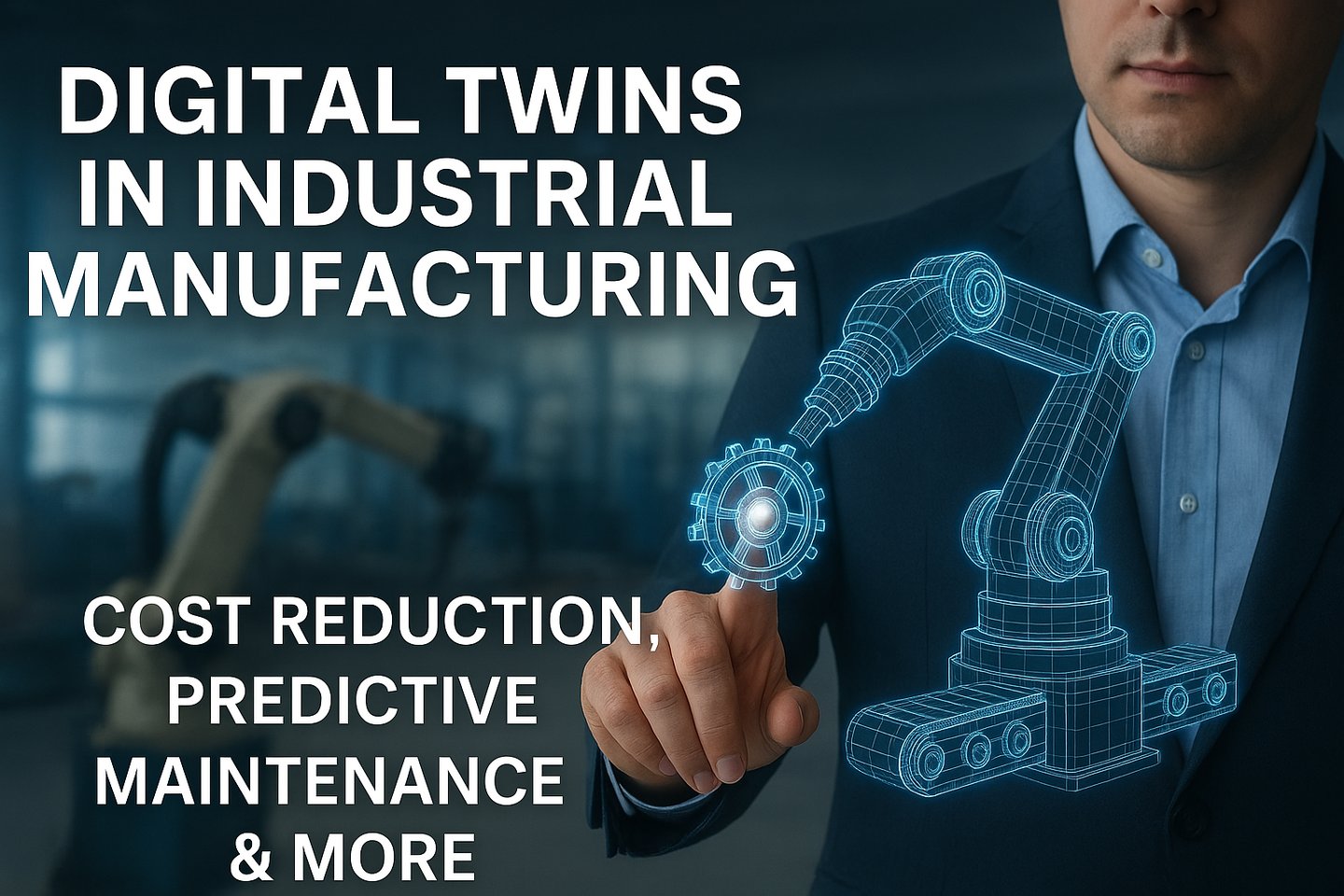
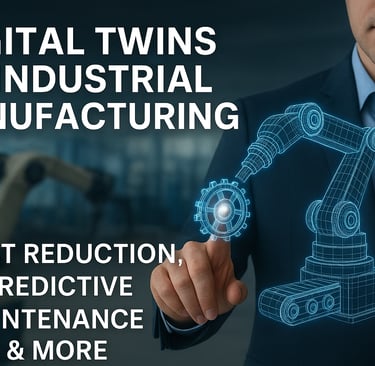
Perfect choice! Here’s the blog post for Herzig Industry Solutions:
How Digital Twins Benefit Industrial Manufacturing: Cost Reduction, Predictive Maintenance & More
In an era where efficiency, speed, and adaptability define success, digital twin technology is revolutionizing how factories operate. More than just a buzzword, digital twins are becoming a crucial component in the future of smart manufacturing — helping companies optimize operations, reduce costs, and make better decisions.
🔍 What Is a Digital Twin?
A digital twin is a virtual replica of a physical object, system, or process. In manufacturing, it can represent an entire production line, a single machine, or even a whole factory. This digital copy is continuously updated with real-time data from sensors and IoT devices, allowing for advanced simulations, monitoring, and control
💰 1. Cost Reduction Through Simulation
Before you build or adjust your production line, you can simulate everything in a virtual environment. This allows you to:
• Identify bottlenecks early
• Optimize machine layout
• Avoid costly design mistakes
• Reduce downtime during implementation
At Herzig Industry Solutions, we support clients with factory planning and layout simulation, ensuring a smooth and efficient setup from day one.
🛠️ 2. Predictive Maintenance
With a digital twin, machines “tell” you when they need attention. This predictive maintenance helps you:
• Prevent unexpected breakdowns
• Extend the life of your equipment
• Save on emergency repairs
• Plan maintenance during low-production periods
Using AI and machine learning, digital twins analyze patterns and alert operators before problems occur — saving money and avoiding production delays.
📈 3. Data-Driven Decision Making
Digital twins gather massive amounts of data from the production floor. You can use this to:
• Monitor performance in real time
• Simulate changes before applying them
• Improve energy efficiency
• Track KPIs and productivity
Data is no longer locked in spreadsheets. It’s visual, dynamic, and actionable — allowing your team to make smarter, faster decisions.
🧩 4. Integration With Smart Factory Concepts
Digital twins are the foundation of Industry 4.0. They work alongside:
• IoT devices
• AI systems
• Augmented reality (AR) for training and maintenance
• Robotics and automation tools
Together, they create a connected ecosystem where every component communicates and adapts to ensure optimal performance.
🤝 Herzig Industry Solutions: Your Partner in Digital Innovation
We help industrial companies transform traditional production into future-ready operations. From planning your factory layout to integrating smart machines and supporting your expansion into the German market — we are your full-service B2B partner.
🚀 Ready to Take the Next Step?
Let’s discuss how digital twin technology can reduce your costs and boost your performance.
Contact us today to explore our solutions for smart manufacturing.
Lösungen
Herzig B2B Beratung & Vertrieb für die Industrie
Freiheitstrasse 124/126 15745 Wildau
Dienstleistungen
Beratung
+49 151 10745292
© 2024. All rights reserved.Herzig
info@herzigb2b.de